Presenter(s)
Suresh Kumar Kanathala
Files
Download Project (814 KB)
Description
This project presents an analysis of various joint types used in variable geometry dies that enable the extrusion of plastic parts with a varying cross section. Extrusion accounts for 40% of all manufactured plastic parts because it is a relatively low-cost and high-production-rate process. Conventional polymer extrusion technology, however, is limited to fixed dies that produce continuous plastic products of constant cross section defined by the die exit profile. A shape changing die allows the cross section of the extruded part to change over its length, thereby introducing the capacity to manufacture plastic faster and with lower tooling costs than injection molding. To allow movement within the die components, various joint designs have been developed. Clearance between the mating parts are required to properly function. These clearances create leakage paths for the plastic melt to escape the die and potentially degrade the quality of the plastic part. Computational fluid dynamics models have been constructed and used to assess the effect of the clearance size on the leakage through the joints. The goal of this analysis is to optimize the geometry of the joints.
Publication Date
4-9-2015
Project Designation
Independent Research
Primary Advisor
Andrew P. Murray, David H. Myszka
Primary Advisor's Department
Mechanical and Aerospace Engineering
Keywords
Stander Symposium project
Disciplines
Arts and Humanities | Business | Education | Engineering | Life Sciences | Medicine and Health Sciences | Physical Sciences and Mathematics | Social and Behavioral Sciences
Recommended Citation
"Joint Design and Analysis of Leakage in Movable Extrusion Dies." (2015). Stander Symposium Projects. 676.
https://ecommons.udayton.edu/stander_posters/676
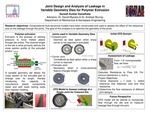
Included in
Arts and Humanities Commons, Business Commons, Education Commons, Engineering Commons, Life Sciences Commons, Medicine and Health Sciences Commons, Physical Sciences and Mathematics Commons, Social and Behavioral Sciences Commons