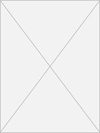
Optimization of Density and Surface Finish in Metal Additive Manufacturing
Presenter(s)
Allyson Meagan Cox
Files
Description
Laser Powder Bed Fusion is a type of additive manufacturing of metal parts that uses fine metal powder that is melted together by a high powered laser, layer by layer, based off a CAD model of the desired design. The metal additive field has gained recent and widespread attention for its innovation, customization, and prototyping. However, due to the nature of industries such as aerospace and defense, the demand for quality products is high. Two ways to measure quality of a finished additive part are density and surface roughness. These properties were measured and compared against changing print parameters to determine process settings that yield optimum part quality. Inconel 718 powder was used in the Advances Technology Laser Additive System (ATLAS) to create test pieces with critical geometries in the design. The individual layers of the part were scanned for profilometry data to analyze internal and edge surface roughness. In addition, the final part characteristics were determined using density testing and metallurgy. During the print, volumetric energy density (VED), mark speed, power, hatch design and part design all remained constant. The number of contours around the edge of the design layer and the offset to hatch were altered for each part. These parameters were compared against each other in the results of the experiment to determine the critical settings of an additive manufactured part that would lead to quality finished parts without post processing.
Publication Date
4-18-2018
Project Designation
Independent Research
Primary Advisor
Jared W. Speltz
Primary Advisor's Department
Additive Manufacturing Tech Develop
Keywords
Stander Symposium project
Recommended Citation
"Optimization of Density and Surface Finish in Metal Additive Manufacturing" (2018). Stander Symposium Projects. 1400.
https://ecommons.udayton.edu/stander_posters/1400
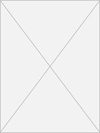