Presenter(s)
Shamsul A. Shamsudin
Files
Download Project (438 KB)
Description
Design of shape-changing machinery is an area of emerging importance. Shape-change may be used in the near future to vary the cross section of a wing, create flow-field control by altering shapes to locally affect downstream fluid behavior, or create extrusion dies with varying cross section critical in a variety of applications including automotive components. The three primary ways of creating shape-change are smart materials, compliant devices, and the focus of this research, rigid body shape-change. Each offers advantages over the other, with rigid body shape-change mechanisms providing the highest capacity to withstand loads and the easiest-to-predict behavior of the three. The goal of this research project has been to modify the synthesis theory to address shape-change where significant differences in arc length motivate the problem. In practical terms, this corresponds to a wing not only changing camber but also changing chord length in operation. The advances proposed here allow rigid-body shape change to address entirely new classes of problems. This is important as rigid body shape-change uses well established mechanical design practice once the bodies have been sized and joints located according to the new theory. These new techniques, combined with the established practice, provide a suite of design tools that allow for problems to be addressed in a fundamentally new way. Shape-changing technology has the capacity to advance manufacturing through an entirely new class of extrusion dies. The design of shape-changing spoilers, beds, wings and chairs are also being considered.
Publication Date
4-18-2012
Project Designation
Graduate Research
Primary Advisor
Andrew P. Murray
Primary Advisor's Department
Mechanical and Aerospace Engineering
Keywords
Stander Symposium project
Recommended Citation
"Designing Planar, Shape-Changing Rigid Body Mechanisms for Profiles with Significant Differences in Arc Length" (2012). Stander Symposium Projects. 150.
https://ecommons.udayton.edu/stander_posters/150
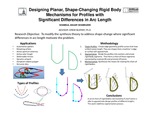