Presenter(s)
Yujie Yang
Files
Download Project (2.0 MB)
Description
Additive manufacturing systems based on selective laser melting of metallic powders are expected to benefit from real-time process control that takes into account measurements of parameters such as the local distribution of powder particle sizes, the texture and roughness of the solidified surface or the actual temperature of the melt pool. We have been investigating fiber scanning imaging systems that operate in such way that they could be incorporated into laser additive manufacturing systems. Laboratory benchtop prototypes for two different imaging systems were built and experimentally evaluated.The first prototype is a confocal imaging system where a single-mode fiber is used for both transmitting the illuminating laser light and receiving the light returning after scattering off the surface of the sample. Its purpose is the measurement of surface characteristics. In this system, the transceiver fiber is mounted to a bimorph piezoelectric actuator, which moves the fiber tip along a line orthogonal to the optical axis and thus also the focal spot across the sample surface. A fiber-optical circulator separates transmitted and received light. A scanner control and data acquisition system allows for continuous recording of line images. Two dimensional images are achieved by moving the sample along the axis that is orthogonal to both the optical axis and the scanning direction of the fiber tip. In the presentation we will discuss characteristics of the obtained imagery and their relationship to surface characteristics of investigated samples.The purpose of the second prototype is the measurement of the local temperature at the melt pool created by the high-power processing laser or at the hit spot of a probing laser for feedback or feedforward control of the power of the processing laser. The measurement of temperature is done by reimaging the sample surface on an infrared receiver fiber and measurement of the power of the received infrared light. One objective of the project is to record infrared (thermal) line images similar to the system described above, but our current laboratory prototype does not yet include a fiber actuator and the electronics for recording of line images. Instead, we demonstrate acquisition of infrared line images of a small sample (a hot wire with 50 µm diameter) by moving the receiver optics with a motorized translation stage.
Publication Date
4-22-2020
Project Designation
Graduate Research
Primary Advisor
Thomas Weyrauch
Primary Advisor's Department
Electro-Optics and Photonics
Keywords
Stander Symposium project, School of Engineering
Recommended Citation
"Fiber Scanning Imaging Techniques for Applications in Laser Additive Manufacturing Systems" (2020). Stander Symposium Projects. 1850.
https://ecommons.udayton.edu/stander_posters/1850
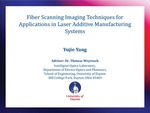
Comments
This presentation was given live via Zoom at 11:00 a.m. (Eastern Time) on Wednesday, April 22, 2020.