Presenter(s)
Khalid Aldhahri
Files
Download Project (1.4 MB)
Description
Liquid Composite Molding (LCM) processes are among the most commonly used processes in composite manufacturing, including resin transfer modeling (RTM) and vacuum-assisted resin transfer molding (VARTM). These types of processes provide several advantages, such as reduced cost, faster cycle time, and efficient part fabrication compared to autoclave molding. RTM is increasingly used to produce composite materials for several applications, especially in the aerospace industry. It offers mass production of composite parts with simple and complex geometry and with small to medium sizes. RTM involved four essential steps to produce the composite part: loading the fiber preform into the mold, injecting the mold with resin, resin curing, and composite demolding. The final composite properties are affected by these steps of production, especially the mold filling and resin curing steps. Numerical process models offer potential benefits for use in LCM, such as improving the mold design, optimizing the location of resin injection gates and vents, controlling the position of the resin flow front, and improving part quality. The main thrust of this study was to demonstrate the effectiveness of simulation applied to RTM for understanding how to choose the right location of injection and vent ports, cure development, and monitoring the position of resin. Numerical modeling allows for initial viewing of the expected flow patterns and cure profiles before the actual resin injection experiment. The commercial PAM-RTM software is used to simulate key process variables, including resin velocity, pressure distribution, filling time, and process parameters. These results will be validated with analytical solutions using Darcy’s Law applied to linear and circular flow models. The model example will be used to compare results of these two approaches for flat panel molds and using two different resin injection strategies for each: constant pressure and constant flow rate.
Publication Date
4-22-2020
Project Designation
Graduate Research
Primary Advisor
Donald A. Klosterman
Primary Advisor's Department
Chemical and Materials Engineering
Keywords
Stander Symposium project, School of Engineering
Recommended Citation
"Resin Transfer Molding (RTM): Analytical and Numerical Approach Development and Verification for a Linear and Radial Flow Model using PAM-RTM" (2020). Stander Symposium Projects. 1975.
https://ecommons.udayton.edu/stander_posters/1975
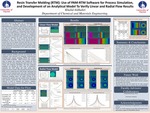
Comments
This presentation was given live via Zoom at 2:00 p.m. (Eastern Time) on Wednesday, April 22, 2020.