Presenter(s)
Braeden Jay Windham
Files
Download Project (536 KB)
Description
Frames used in aircraft and automotive structures must be rigid and lightweight. With modern software, frame designs that are optimized for stiffness with respect to weight can be readily generated. Manufacturing these frames, however, can be costly and difficult. The purpose of this research is to accept the optimized frame results from the design software and pass them through an interpreter to create a frame that is akin the optimized result, but manufacturable with off-the-shelf components. Along with being more manufacturable, this process also eliminates variation in the final design associated with the frame being interpreted differently by different engineers. This optimization process, called topology optimization, begins with a specified design space, applied loads, and constraints. Within the design space, material is strategically removed in order to maintain the optimal stiffness with respect to weight. From there, the generalized shape is interpreted as an arrangement of members and nodes, which are places that two or more members meet. This information is then passed to a second optimization process that changes the size and geometry of the member and node locations to maintain an optimal shape. With the frame now optimized for stiffness as well as being manufacturable, an automated process generates a design model within SolidWorks with structural tubing and welds so that the physical frame can be created.
Publication Date
4-22-2021
Project Designation
Independent Research
Primary Advisor
Andrew P. Murray, Dave Harry Myszka
Primary Advisor's Department
Mechanical and Aerospace Engineering
Keywords
Stander Symposium project, School of Engineering
United Nations Sustainable Development Goals
Industry, Innovation, and Infrastructure
Recommended Citation
"Topology Optimization Frame Interpreter" (2021). Stander Symposium Projects. 2381.
https://ecommons.udayton.edu/stander_posters/2381
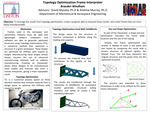