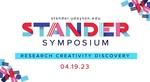
In-situ Optical Surface Feature and Temperature Sensing System for Selective Laser Melting (SLM) Technology
Presenter(s)
Yujie Yang
Files
Description
We describe techniques and present results for in-situ monitoring of surface features and temperature that can operate in challenging environments near laser-material interaction locations. The techniques are considered for incorporation into laser material processing systems such as for laser welding or additive manufacturing of metallic parts with powder bed selective laser melting (SLM). Surface characterization is performed using a fiber-based line-scan confocal optical system, where a laser beam is transmitted and received by a fiber whose tip is affixed to a piezoelectric actuator that changes the lateral position of the fiber tip at a rates up to several kilohertz. Characteristics of the power of the received laser light depend on surface properties and can be used to classify surface roughness, for instance with the help of machine learning (neural networks), or to identify anomalies or defects at the surface. The temperature sensing approach uses a similar line-scanning optical system, but in a passive configuration, where the received light is thermal radiation emitted from the surface under test. The line scanning of the receiver fiber tip allows for generation of temperature profiles, for instance in the vicinity of the melt pool in SLM systems.During the SLM process, there are some critical parameters that must be monitored to ensure the quality and integrity of the final part. In-situ surface monitoring and temperature sensing are particularly important. In-situ surface monitoring can detect defects or irregularities as they occur, allowing for immediate corrective action and it can also help to ensure that the part is being built correctly, by verifying that the dimensions and features of the part are within acceptable tolerances. By monitoring the temperature in real-time, operators can adjust the laser power, scan speed, or other process parameters to maintain the optimal temperature range for the specific material being used.
Publication Date
4-19-2023
Project Designation
Graduate Research
Primary Advisor
Thomas Weyrauch
Primary Advisor's Department
Electro-Optics and Photonics
Keywords
Stander Symposium, School of Engineering
Institutional Learning Goals
Scholarship; Scholarship; Scholarship
Recommended Citation
"In-situ Optical Surface Feature and Temperature Sensing System for Selective Laser Melting (SLM) Technology" (2023). Stander Symposium Projects. 3224.
https://ecommons.udayton.edu/stander_posters/3224
Comments
Presentation: 1:00-1:20 p.m., Jessie Hathcock Hall 101