Presenter(s)
Khalid Aldhahri
Files
Download Project (1.6 MB)
Description
Resin transfer molding (RTM) is a manufacturing process used to produce high-quality composite parts that offer exceptional high strength-to-weight ratios, superb stiffness, and excellent resistance to corrosion and fatigue. These composites are typically comprised of carbon or glass fibers infused with a liquid thermosetting resin that hardens during a high temperature cure cycle. To produce RTM products, a matched metal mold is usually required. The mold cavity is shaped to the desired geometry of the finished composite part, and channels or gates allow resin to flow into it. In reference to cavity mold design, there are many challenges in terms of resin injection gates, vents, and resin flow directions, both in terms of filling time and the flow dynamics of the materials. These issues often require many costly iterations to perfect the cavity design for a given part. This study focuses on the use of AM in developing and fabricating plastic prototype molds that can be used to produce a limited number of finished composite parts, such as T-joints, canted T-joints, and I-beams. This approach allows for rapid and low-cost iteration of composite designs prior to investing in expensive finished metal tooling.
Publication Date
4-19-2023
Project Designation
Graduate Research
Primary Advisor
Donald Klosterman
Primary Advisor's Department
Chemical and Materials Engineering
Keywords
Stander Symposium, School of Engineering
Recommended Citation
"Use of Additive Manufacturing in Developing Advanced Composite Structures Fabricated by Resin Transfer Molding" (2023). Stander Symposium Projects. 3247.
https://ecommons.udayton.edu/stander_posters/3247
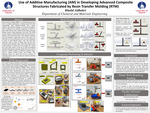
Comments
Presentation: 1:15-2:30 p.m., Kennedy Union Ballroom