Presenter(s)
Alex M. Watt
Files
Download Project (869 KB)
Description
Polymer extrusion is a manufacturing process of forcing a melted plastic through a die to create a continuous part with a constant cross-section dictated by the die’s geometry. The typical process uses a fixed die that creates high output at low cost when compared to injection molding. The overarching goal of this project is to develop dies capable of changing cross sectional area during the extrusion process. Preliminary dies have been designed, created and operated in a production process. In order to test the shape repeatability of these dies, a laser scanner was used to capture cross sections at numerous locations along the resulting parts. A numerical process was then developed to accept the data from the scanner and create a representation of the profile. These profiles were then compared to the profiles at other locations. The repeatability of the sections from these variable geometry parts has been found to be similar to fixed-geometry parts. Further, the extruded parts have also been compared to the die exit geometry to examine expansion that occurs during the process.
Publication Date
4-9-2015
Project Designation
Independent Research
Primary Advisor
Andrew P. Murray, David H. Myszka
Primary Advisor's Department
Mechanical and Aerospace Engineering
Keywords
Stander Symposium project
Disciplines
Arts and Humanities | Business | Education | Engineering | Life Sciences | Medicine and Health Sciences | Physical Sciences and Mathematics | Social and Behavioral Sciences
Recommended Citation
"Assessing Shape Repeatability in Variable Geometry, Polymer Extrusion Dies" (2015). Stander Symposium Projects. 633.
https://ecommons.udayton.edu/stander_posters/633
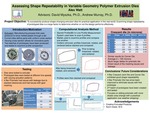
Included in
Arts and Humanities Commons, Business Commons, Education Commons, Engineering Commons, Life Sciences Commons, Medicine and Health Sciences Commons, Physical Sciences and Mathematics Commons, Social and Behavioral Sciences Commons