Presenter(s)
Heather M. Smith
Files
Download Project (922 KB)
Description
Conventional polymer extrusion is a common manufacturing process in which plastic resin is melted and pulled through a fixed-geometry die plate to produce a shape. This process creates long parts with a uniform cross-sectional area, including pipes, molding, and window frames. Shape-changing dies would expand the capabilities of extrusion by allowing the cross-sectional area to change over the length of the extruded part. This would allow for parts manufactured more quickly and at a lower tooling cost, as compared to other processes such as injection molding. A constant extruder screw speed is desired throughout the process due to the pellets being melted by friction within the screw. As the area of the orifice changes throughout the extrusion, problems arise which may be pacified by varying the line speed, or tracking differences between the final shape and the exit area of the part. The goal of this project is to design a series of variable extrusion dies that exhibit significant changes in area. Three types of die were created, each evaluating a different strategy, including bypass ports and shape modifying features beyond the die exit. The dies have recently been produced, installed, and tested to evaluate the various features of each design.
Publication Date
4-9-2015
Project Designation
Independent Research
Primary Advisor
Andrew P. Murray, David H. Myszka
Primary Advisor's Department
Mechanical and Aerospace Engineering
Keywords
Stander Symposium project
Disciplines
Arts and Humanities | Business | Education | Engineering | Life Sciences | Medicine and Health Sciences | Physical Sciences and Mathematics | Social and Behavioral Sciences
Recommended Citation
"Variable Extrusion Dies that Exhibit Significant Change in Exit Area" (2015). Stander Symposium Projects. 670.
https://ecommons.udayton.edu/stander_posters/670
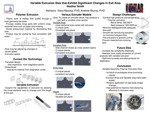
Included in
Arts and Humanities Commons, Business Commons, Education Commons, Engineering Commons, Life Sciences Commons, Medicine and Health Sciences Commons, Physical Sciences and Mathematics Commons, Social and Behavioral Sciences Commons